GEMSTAR TEAMS UP WITH A DOD CONTRACTOR TO ENGINEER A SOLUTION FOR THE U.S. ARMY
Published: May 2023
When a prime military contractor contacted Gemstar about developing a custom hard case for the U.S. Army’s new light armored vehicle platform, they knew Gemstar would be up for a challenge.
In this case, the challenge was developing a custom hard case to securely hold a critical component of a mobile weapon system in the tight confines of the U.S. Army’s Stryker light armored vehicle.
“When you’re competing for space within the cavity of a light armored vehicle,” said Barry Birkholz, Director of Technical Packaging for Gemstar, “every inch truly counts.”
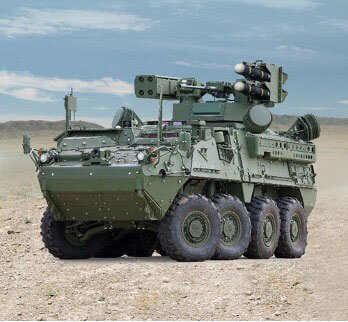
KEY CHALLENGE: OPTIMIZE SPACE
The prime contractor to the Department of Defense (DoD) was awarded a contract to design and manufacture a storage container to hold the Gripstock firing mechanism for a short-range air defense missile system, which is operated by a single soldier who travels in the Stryker vehicle.
In the initial scope of work, the storage case needed to fit within a tight space – 32" x 12" x 15" – on a shelf in the cavity of the vehicle, within easy reach of a soldier.
ENGINEERING A SOLUTION
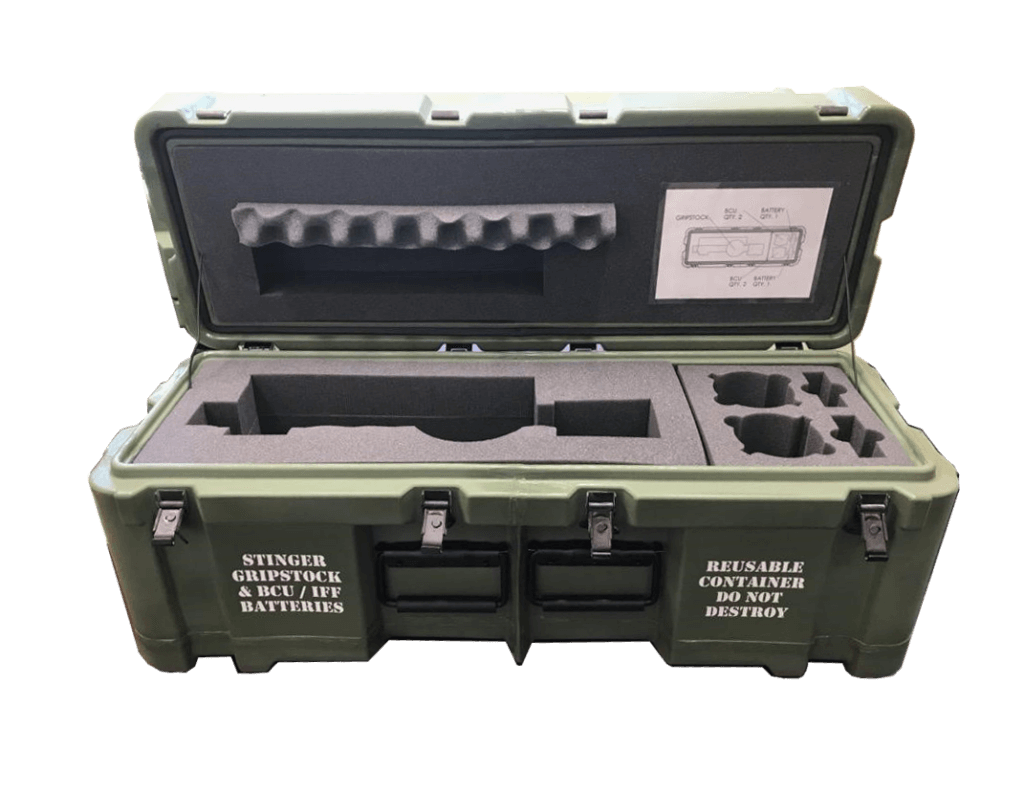
The process of designing a custom solution begins by developing a close relationship with Gemstar’s customers.
“We work closely with our military customers to deliver exactly what they need,” said Birkholz. “Our engineers are passionate about identifying solutions that protect high value parts and components.”
For this project, there was only one solid choice to meet the exacting demands of the U.S. Army – the Stronghold® case by Gemstar.
Gemstar’s engineering team met the challenge, developing a hard case that was 28" x 8" x 8".
Beyond optimizing the size of the exterior of the hard case, Gemstar engineers also recommended:
• Customizing the interior to meet a static load requirement
• Inserting another handle in the center of the front case
• Designing the container with a hinged lid
• Adding a placeholder for future accessories
• Customizing foam cushioning
• Adding a custom metal label
• Including custom stenciling
• Adding internal labeling for content placement
• Designing the case for a single soldier to handle
Prototypes were created utilizing Gemstar’s cut-and-weld raid prototype program. The prototypes were field tested to prove they met the rigors of the MIL STD 810 standards and to pass a static road requirement.
“These prototypes were delivered within two months after the scope of work was issued. Then the prototypes were tested by actual military personnel in the field for more than a year.” said Birkholz.
STRONGHOLD: MANUFACTURED WITH EXCLUSIVE ROBOMOLD TECHNOLOGY
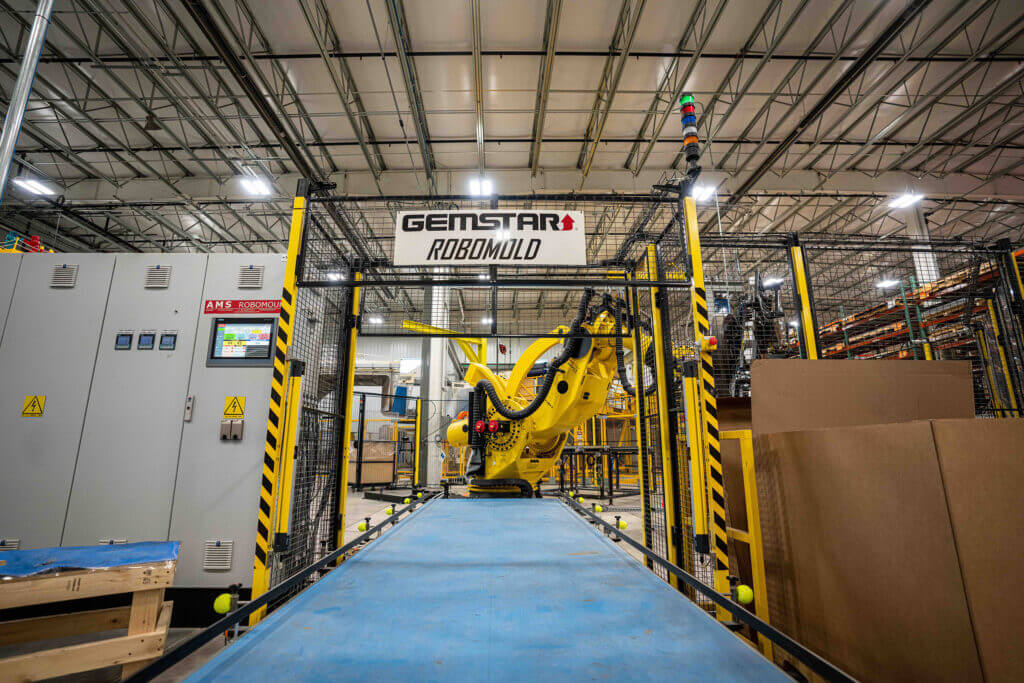
The Stronghold® 2808 hard case series was the first case created exclusively on Gemstar’s proprietary Robomold® robotic rotational molding technology for production.
Stronghold double-walled cases boast GSR™ high performance resin, patented latches, rubberized spring-loaded handles, recessed hardware, and interlocking stackability. This military-grade hard case is designed and tested to meet or exceed MIL-STD 810F and military Long Life Reusuable Case (LLRC). These cases are airtight and watertight. Most importantly, they can be customized internally to ensure proper protection of sensitive assets. Stronghold cases are currently available in 134 sizes and configurations.
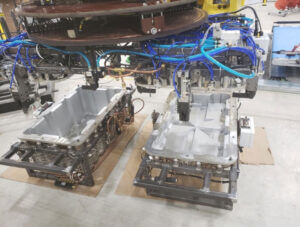
Robotic rotational molding is a leading-edge technology that’s ideal for military, OEM, industrial, and commercial applications where precision and repeatability are essential. Robomold technology creates high tolerances with precision-distributed heat and material control for consistent plastic part repeatability and optimized strength-to-weight ratios. This technology allows for unsurpassed design flexibility, including the ability to layer different compounds and coatings into finished parts where conventional rotational molding cannot satisfactorily meet evolving design requirements.
Printable version click here.
READY TO SERVE AMERICA'S MILITARY
Gemstar designs and manufactures hard cases specifically for military applications. To learn more about Gemstar’s expertise in military and government applications call us at 800.533.3631.
ABOUT GEMSTAR
Gemstar Manufacturing is an engineering-based solutions provider with 60 years of manufacturing experience and knowledge. The company is a family-owned business supported internally by long-term employees. The firm’s history is rooted in custom manufacturing and the dedication of a customer-centric organization. Gemstar’s mission is “to test the limits of plastic manufacturing and exceed the expectations of customers,” which is shown through their dedication to provide value add solutions to customers through innovative design and technology.